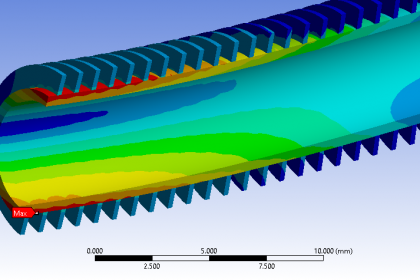
You might be surprised to learn that there are a wide variety of answers to this question. Beyond the shear versatility of this powerful tool, opinions on the matter vary significantly. Some believe finite element analysis is only for product development. Others feel it is only useful early in a design process. Specialists such as myself have a unique viewpoint . We see engineering products across industries, company size, project types, both in product development and failure analysis. FEA shortens project lead times, improves robustness, and saves money. Here’s how .
Take a moment to consider all the work that goes into building and testing a prototype. It’s typically labor intensive, costly, and time consuming. You’ve got vendors to manage. The assembly process is not fully developed. Geometry is not finalized. The finished product is an awkward and imperfect representation of a design that isn’t fully defined yet. Now try to build enough of these to test in a variety of ways and hope that the results provide meaningful design guidance.
Also consider the testing that must be performed. You might have a lab in house, but anything large or complicated is typically outsourced. There are vibration test houses, enormous thermal chambers, or even very small features that must be loaded specifically. As with prototypes fabrication, test outsourcing is expensive, carries long lead times, and requires significant hand holding. Additionally, tests are often performed in isolation or at best using an incomplete set of loading conditions to represent the real world. Results are ambiguous at best. Sometimes realistic tests can’t even be run due to safety or logistical concerns. Here’s where simulation can add significant value.
FEA can be used to evaluate and compare competing design configurations. Complicated and nuanced loading conditions can be applied, and product performance can be evaluated. An extremely high number of iterations can be run in the same time it takes to build a rough prototype and run a simplified test. Weighing iterative testing against iterative simulation, the cost and time savings quickly become apparent. Once a model is set up, the only cost is simulation run time.
Testing will always be necessary. In a perfect world, however, we’d only run two tests . The first would calibrate our FEA model. The second would be our pre-launch verification and validation tests. Naturally, the optimal position is typically somewhere in the middle, but leveraging this powerful tool will improve project outcomes.
There is a sample finite element analysis on the Focused Engineering website here. It illustrates how FEA can not only be used to design an individual product, but also the larger system it fits into. It also highlights how iterative use will save time and money. Take a moment to see for yourself!