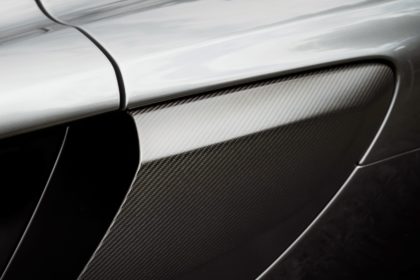
Think you’re up to date on the latest in design, analysis, and fabrication of parts and assemblies using composite materials? If most of us are honest with ourselves, our practical knowledge may be more limited than we realize. Here is a helpful primer on the latest in the world of design, analysis, and fabrication of parts using composite materials.
MATERIALS
Composite materials essentially always come down to fibers and resin. Fibers of varying material, length, spacing, and pattern are embedded in a matrix material. Both the fibers and matrix material contribute to aggregate strength. Demonstrating high strength and low weight, these materials exhibit behavior and failure modes that are drastically different than traditional materials like metals. Fibers can be short, medium, or long. They can have well ordered directions and patterns or they can be chaotic and random. Resulting material properties are also as much a function of fabrication method as they are of component raw materials.
FABRICATION
There’s a dizzying number of production techniques used to make components and assemblies, and part strength is significantly affected. Fibers can be woven, wound circumferentially, laid unidirectionally in sheets and laid up in plies. Additionally, fiber density and included angle can vary when plies are wrapped and formed or compressed around irregular shapes. Layers can abruptly start and stop in the middle of the layup, and this can create a failure initiation site. Understanding the fabrication method and modeling it as closely as possible is essential to obtaining useful results.
ANALYSIS
ANSYS Mechanical includes a composite pre / post processor module that captures all of the above in a realistic way. Flexibility in inputs and outputs is extensive and includes the following:
- Define the number of plies, ply thickness, fiber direction within plies, and ply starts and stops building out from any complex 2D surface object
- Use full 6×6 stiffness matrix anisotropic material properties (different in every direction) or use simplifications based on symmetry in fiber patterns (e.g. only 9 constants for orthotropic and 5 for transverse orthotropic patterns)
- Use 2D shell elements in meshing for plane stress (no stresses in the third direction) or 3D solid elements for thicker areas often associated with plane strain.
- Auto-draping to determine fiber direction where appropriate
- Control over whether to use matrix material properties at layer ends or not (more conservative not to)
- ANSYS can create a ply book that can be used to generate manufacturing documentation
- Predict failure using 10 different methods that can look at max tensile, compressive, and shear stresses, first fiber fractures, matrix material failures, and even delamination, crack growth, and progressive failure. Results can also take core specific failure into account.
- Specialized graphics facilitate layer by layer inspection per each criteria
Composite materials are indeed well understood and widely used, and yet there continue to be inspiring innovations. It’s both fascinating and fun.